How to market BATCH
Identify anyone who is or could be a stakeholder these will include the following:
• Clients
• Suppliers
• Developers
• Builders
• Estate agents
• Government bodies
• Councils
• Industrial bodies
• B.R.E
• M.P’s
• Planning consultants
• Key developer
To engage with your stakeholders hold a launch event.
Produce a press release.
Attend events that are relevant to your business. These may include:
• National home improvement show
• Future energy show
• Any shows that developers may attend
You can give people more confidence in your company and use recognised logos by joining industry bodies such as:
• Green Building Council
• C.I.B.S.E
• I.C.E
You should perform a competitor analysis. (SWOT)
In order to promote the company you should produce:
• A video
• Brochure
• Animation
• Postcard
• Website
• Business cards
You should have a social media plan that is updated regularly this should include the following:
• Twitter
• Facebook
• Linkedin
You could also consider writing features for or advertising in the following:
• National journals
• Trade press
• Property Week journal
• Any planning journal
More students. Families are becoming more separated with more single parents – Divorce isn’t as taboo as it used to be.
What types of accommodation do people want? Apartments, terraced housing, semi-detached housing, detached housing
How can you make it possible to customise standard models of developer housing without it becoming a bespoke and ‘architect’ designed individual project?
Palettes of materials and finishes?
Newsletter/mailing list
Stakeholders
Individuals looking to build/buy a home
- First time buyers,
- Those on a lower income
Small Land owners looking to benefit by renting/developing out the land i.e. A farm owner.
Manufacturing/Supplier Company
- Connections with construction teams by each colleague from previous work experience.
- SKANSKA
- BSW Timber Group
- Willmott Dixon
- Walker Timber Group
Future collaborations with developers
- Taylor Wimpey
- Barratt Homes
- Berkley Group
- Places for People
- Miller Group
- Bellway Group
Construction categories
- Kier
- Carillion
- Laing O’Rourke
- Mitie
- Interserve
- Balfour Beatty
Estate Agents
- Haart
- Savills
- Rightmove
- Your move
- Bairstow Eves
- Connells
Councils
B.R.E
National House Building Council
RIBA
CIOB
M.Ps
Planning consultants
Central Government
A launch event can be held to engage with these stakeholders and promote the product.
Attend events relevant to target market in order to expand the customer base such as: National home improvement show, future energy show, Ecobuild, National Home building and renovation show.
Press release
With housing prices back on the increase after the economics crash of 2007, one could assume that this growth would continue and by 2020 there would be a thriving market, with enough room for new businesses to be established and succeed.
- In the 12 months to December 2012 UK house prices increased by 3.3%, up from a 2.2% increase in the 12 months to November.
- House prices have increased across most of the UK in 2012, although prices in Northern Ireland have continued to fall.
- The year-on-year increase reflected growth of 3.4% in England, 2.4% in Wales and 3.1% in Scotland, which were offset by a decline of 5.7% in Northern Ireland.
- Annual house price increases in England were driven by a 6.4% rise in London and a 3.7% increase in the South East.
- Excluding London and the South East, UK house prices increased by 1.9% in the 12 months to December 2012.
- On a seasonally adjusted basis, UK house prices increased by 0.9% between November and December.
- In December 2012, prices paid by first-time buyers were 2.7% higher on average than in December 2011. For owner-occupiers (existing owners) prices increased by 3.5% for the same period.
1. Land
You have land and a project in mind. If you are thinking of buying a plot and want to get a feel for likely costs then why not look at our standard designs.
2. Planning permission
Already have planning – go to 3.
If you don’t yet have planning permission then we offer a full planning service.
3. Plan your project
Whilst waiting for planning permission this is the ideal time to plan your project. We will provide a detailed costing for the supply only, or supply and construction of your building kit.
We normally supply a completed building shell to an agreed specification for construction on a prepared foundation. You will need to decide if you are going to manage the build yourself, use a full-time project manager or architect to supervise the work or a single contractor in which case we are happy to work as a nominated supplier.
4. Order your kit
When you are ready to get started we will ask you to approve the final drawings for production. We will provide structural calculations and construction detailed drawings as required for building regulation approval.
For timber frame panel buildings we will also need to work through details such location of electrical outlets, as well as plumbing and waste outlets as these service are pre-installed in the factory.
Delivery is generally between 4 and 8 weeks depending on the complexity and seasonality, during this time the site can be prepared including foundation and ground works.
5. Delivery, build and handover
Your kit will be delivered to site. Construction normally takes between one and three weeks. At the end of the build we will ask you to approve the building before we handover to your for the trades e.g. roofers, electricians, plumbers to start work on the building.
Eventual expansion in to global markets, starting with European countries then further afield.
A future development of the company could be to eventually become an ethical developer where large numbers of houses can be constructed on one site and customised by collaborating with potential customers.
This is not viable currently because developers wouldn’t be prepared to settle on a plan for fewer houses just so they can satisfy customers as they wouldn’t make as much money. Because no developers are offering any alternatives to the mass-produced impersonal ‘boxes’, the public accept what is being produced and are still prepared to pay money for them.
Trends in Net additional dwellings
Seasonally adjusted trends in quarterly housing starts and completions, England.
Starts experienced a period of sustained growth from 2001 until 2005. From 2005 starts were broadly steady, averaging around 44,000 units each quarter until late 2007. Completions increased gradually from 2001 reaching a similar level to starts by 2007.
Starts were strongly affected by the economic downturn and from the start of 2008 there was a period of rapid decline to a trough in the March quarter of 2009. Completions fell more slowly than starts but over a longer period. From 2009 starts began to recover and during the next two years both series converged and levelled out. Despite fluctuations house building has remained at a broadly constant level for the past 11 quarters.
The UK's high house prices are a drag on its economy; they hamper movement, encourage boom and bust and leave it vulnerable to shocks. Narrowing the gap between property prices and wages and making buying a home less of a gamble, would be a good thing.
Raising a deposit is the most significant barrier to moving up the property ladder – £58,836 is now needed, almost double the £31,189 required a decade ago – preventing three in five first-time sellers from trading up.
House building is crucial to economic recovery. From the Depression of the 1930s, through the rebuilding of Britain after the Second World War, to every recession since, politicians of all parties have recognised the need to build our way out of economic crisis
House building is at its lowest peacetime level since the 1920s.
Because those trying to buy a second home cannot afford to do so, those trying to buy their first home are building up, creating a ‘bottleneck,’ which needs to be dealt with in order to maintain a flow in the housing market.
40% of people hoping to buy their second property this year are living in homes their families have outgrown.
Three USPs
Affordability – Even after buying the land the price is less than a standard developer home. £80,000 typical.
Customisation – Build size, layout and aesthetics are tailored to the needs of the client and the constraints of the site.
Speed and quality of construction – Factory made so the product can be airtight and al components will fit together perfectly. No delays such as weather delays because it is produced indoors. Groundwork such as foundations, water, gas and electricity can be done on site during the production of the pre-manufactured components prior to them being delivered.
House building usually only starts to pick up towards the end of spring and throughout the summer, very little actually takes place during the winter and early spring because of the weather. This type of construction can continue year round because it is only restricted by the weather on a very minor scale.
Sustainability – Timber is more sustainable than masonry, steel and concrete as more trees can be grown in place of the ones that are cut down for the manufacture of a BATCH building.
Political – The government has emphasised the lack of accommodation and it’s desperation to find a way so that no one is without a home and establish an accessible to all method to make it easier to house the ever-growing population. – How will the population have increased by 2020?
Strong objectives have been set regarding sustainability and the aims to become even greener and environmentally friendly.
Economic
Social
Technological
Environmental
Legal
People: From the receptionist answering the telephone to the contractors employed to fulfil building projects on behalf of BATCH Architecture all employees and associates of the firm are stakeholders in the business and will deal with clients in a polite, friendly, prompt and efficient manner.
Process: (insert your information here)
Place: Much of BATCH Architectures business will be generated through the website. In general appointments will be made to visit clients at their site rather than people ‘dropping in’ to discuss their architectural requirements, this does not mean that the office can be in the middle of no-where; it will be positioned on the outskirts of the city. The building will be a good example of BATCH's architectural ethos giving client’s confidence in the product.
Product: (insert your information here)
Physical presence: The name ‘BATCH’ and the company logo indicate the concept of the firm. These will be used on the website, on social media websites, business cards, letterheads and advertising and promotional materials; they could also be used on company cars and awnings at sites where building will take place.
Price: This will be a major factor as BATCH design buildings using pre formed panels (SIPS) that are customised to each client’s requirements. This will reduce overall costs to clients. (insert your information here)
Promotion: BATCH Architecture will register with the Architects Registration Board so that people looking on the internet for an architect in the local area automatically have access to BATCH’s details. Advertise in telephone directories and any locally produced publications such as ‘Life magazine’ and ‘Nottingham Life and Countryside Magazine’. Advertise in national magazines such as ‘Self Build’. Attend shows nationally and locally such as the ‘Home building and Renovation Show’ recently held in Birmingham.
Tailor-made, Mass-produced.
European Federation of Pre-manufactured Building
• Eight national members Austria, Bulgaria, Germany, Great Britain, Hungary, Ireland, Sweden and Switzerland.
• More than 3 million buildings or approx. 20.000 pre-manufactured buildings per year – mainly one and two family homes.
• Principle = Promotion of competitiveness of pre-manufactured construction in timber.
Huf-Haus are a leading company in the manufacture of customisable, mass-produced, pre-manufactured timber architecture (homes, offices, industrial).
• They also provide services for the customisation of interior fittings and spaces such as gardens.
• They offer tailor designed financing for the homes they provide.
• Environmental and climate protection through the continuous improvement of energy efficiency both in current manufacturing processes.
• Planning, building, financing, fitting-out and handing over a ready to occupy, highly customised HUF house to the customer is a complex process.
A home will be one of the if not the most expensive and valuable possessions a person invests in. Although they could always move house, they should be able to start with something perfect right from the beginning.
A pre-manufactured timber frame building contributes massively towards energy saving and building quality.
What is our product?
Pre-manufactured, tailor made, mass-produced architecture.
Is there a big enough market for this business?
Market
There are five competing concepts under which organizations can choose to operate their business; the production concept, the product concept, the selling concept, the marketing concept, and the holistic marketing concept. The four components of holistic marketing are relationship marketing, internal marketing, integrated marketing, and socially responsive marketing. The set of engagements necessary for successful marketing management includes, capturing marketing insights, connecting with customers, building strong brands, shaping the market offerings, delivering and communicating value, creating long-term growth, and developing marketing strategies and plans.
A total number of more than 3 million buildings or approx. 20.000 pre-manufactured buildings per year – mainly one and two family homes.
Big markets for timber pre-manufactured housing in Scandinavia/other colder climate countries due to insulating properties of timber and the fact that this type of construction is very energy efficient.
Online design options/selection, like the specifications for a car, whether you want air conditioning, built in satnav or the colour you choose. Keeping the cost down and giving the customer choice.
A pre-manufactured house is a building that is built on a prepared basement. It consists of prefabricated, storey-high panel walls, modules, and prefabricated ceiling and roof sections, which are manufactured in factories, protected from weather conditions and which are transported to the construction site.
Despite this, roof constructions including their ceiling constructions can be without prefabrication because of special architecture.
The UKTFA is the trade organisation representing over 85 % of UK timber frame manufacturers and also the sectors key suppliers.
Modular construction
▪ Overall build programmes reduced by up to 50%
▪ Rigorous quality control
▪ Cost certainty
▪ Programme certainty
▪ Continuous investment in cutting-edge technology, research and development
▪ Reduced defects and snagging
▪ Weather disruption significantly reduced
▪ Health & safety risks reduced
▪ Impact on client's operational activities minimised
▪ Site traffic reduced by up to 90%
▪ Less impact on the local area
▪ Ideal if site access roads or site contractor space is restricted
▪ Customised solutions tailored to clients needs
▪ Built from sustainable and recyclable materials
▪ Available for sale or hire
▪ Hire option can have significant financing advantages
▪ Economical to maintain
Turnkey solutions
India is an emerging market for pre-engineered buildings, industrial, warehouses and automotive construction domains, 80% in pre-engineered steel.
Particular growth in pre-engineered retail outlets, such as those for supermarkets.
Residential has the lowest market share of PEBs.
Terrapin Developers – Offer modular construction solutions.
Premier Interlink (WACO UK Ltd)
To convince the bearer that this piece of paper has value equal to the quantity of gold it once represented, it is dressed up with antique typefaces, scrolls, swags and cartouches, giving an impression of continuity and historic grandeur. The note is interchangeable and mass-produced, and when economic crisis hits, is hardly as reliable as it looks – so that appearance is all the more important. – Metaphor of mass-produced housing.
The price of most other things, from food to cars, have reduced as production processes become more ruthlessly efficient, but housing has become more and more expensive
Mass production might be easier to deal with if it comes with a house, garden and car-parking space.
Anywhere you might be expected to live in for more than nine months must preferably be built in much the same way as a house was built in the 18th century, in case anyone gets scared, whether builders or buyers.
The reason for this persistent failure to rationalise housing, to make it into a product like any other, might be because it tries to rationalise something – the property market – that is inherently irrational. Homes can't be products, they're too important to a dysfunctional economy. If they stopped being quite so archaic and mythical, but became instead something easy and cheap, then the entire bubble might finally burst.
BOKLOK – Ikea’s branch that develops modular buildings.
Design by architects who understand how to create comfortable homes and interior designers who understand how people want to live.
Designed around factory processes – More efficient construction.
Who are the customers?
How much can they afford without having to change their lifestyle elsewhere?
How do they want to live?
Find statistical information about the size and types of people using these buildings and how it will change, i.e. the composition of households.
Income
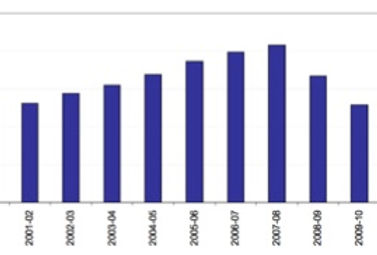
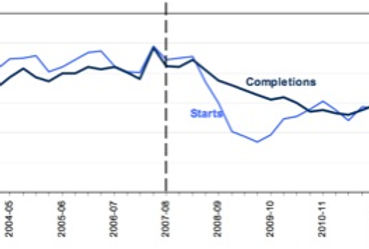